Material Handling
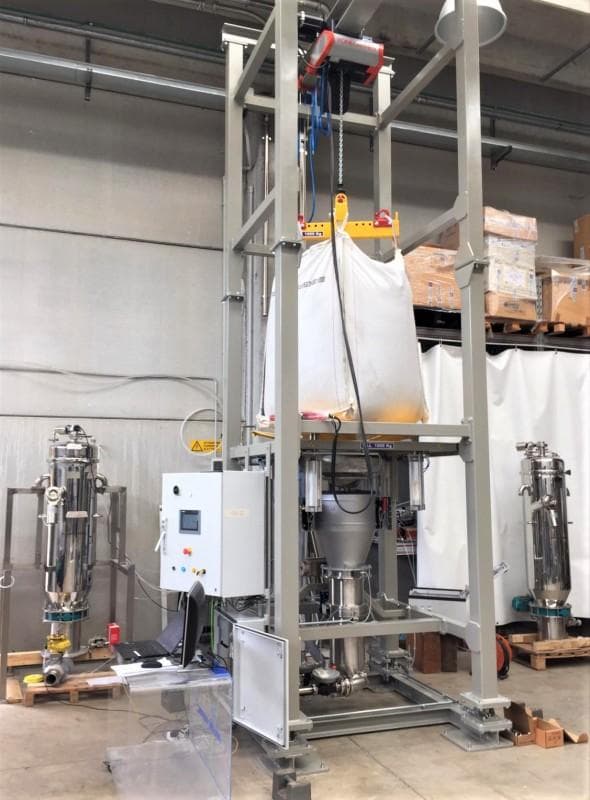
Mechanical Conveying
Mechanical conveying systems are suitable for bulk handling across a range of industries as it effectively transports product horizontally, vertically, and even at incline through the production line. This system is very suitable for high capacity conveying rates and for handling different materials like abrasive products. To allow the transport process, there are typically number of moving parts within a mechanical conveying system including belt, buckets, chains and trays that are utilized to move product at a controlled fast pace.ETST offers a wide range of mechanical conveying systems, having major variety of possible applications for dosing, discharge, powders conveying, granulates from hoppers, silos, bag empty systems and many more.Types of Mechanical Conveying:Screw Conveyor- is used for conveying or feeding powdery or granular materials which is designed for application in which any contamination of the material handled has to be strictly avoided and where absolute cleanliness and perfect resistance to corrosion are required, usually in the food industry. This system is often used for moving materials from hoppers, bin, or silos at a controlled rate and volume.Belt Conveyor - is used for conveying sensitive or corrosive materials across a short straight run, ensuring no mechanical friction and using only low energy consumption. Belt conveyors varies from drive and bed types, load to be conveyed and conveyor speed. Bucket Elevator - it is the vertical elevation of bulk materials which can be equipped with numerous configurations such as centrifugal belt, centrifugal chain, continuous belt and continuous single or double chain. The material is introduced into a loading hopper then continuously picked up by buckets to an endless belt, the buckets are discharged through an outlet spout in the head section by centrifugal force after having passed the upper roller wheel.
Vacuum Conveying
The vacuum is used with great advantage in conveying bulk dry materials like powders, from place to place through suction to dedicated pipe systems. It can be used in production for a load of mixers, mills, dryers, batching machine, bin, etc., and packaging for a load of filling machine, tabletting machine and many others. Vacuum Conveying is widely used for short-distance conveying to prevent dust contamination of production facilities. The material is transferred from the receiver to its final destination with numerous methods usually done using slide vales, pneumatically operated dump gates and airlock rotary valves, depending on the application. ETST is experienced in vacuum conveying of plastic polymers, calcium chloride, sodium bicarbonate, sodium bisulfate, and other dry materials. When applied with food, pharmaceuticals and chemical products, ETST ensures the highest possible degree of safety as to hygiene and operation. Contact us now to assist you with your vacuum conveying requirements.
Positive pressure conveying
Positive pressure systems are suitable for conveying bulk materials at low to moderate capacities from one source to multiple pickup points to go to multiple destinations over medium distances. Positive Pressure Conveying System usually consists of positive displacement air blowers and a rotary valve to serve as the power source. There are three main categories as follows: dilute phase, dense phase and semi-dense phase. Dilute Phase - Dilute phase pressure conveying is the process of pushing or pulling air-suspended materials from one location to another by maintaining a sufficient airstream velocity. Dilute phase pressure conveying is essentially a continuous process, characterized by high-velocity low pressure and low product to air ratio. These systems are versatile and adaptable for different materials and the low operating pressures allow lower-cost pipelines and fittings. Some of the examples of products that can be conveyed successfully using this method are cement, fly ash, food items, resins, dry chemicals and many others. Dense Phase - Dense phase pressure system is practically appropriate especially when handling products which are fragile, have a tendency to segregate, or are temperature or moisture sensitive, due to their ability to convey efficiently at long distances and high capacities. This system uses compressed air to push materials from a pressure vessel, sender unit or pressure pot through a pipeline to a destination where the air and product are separated. Valves and sensors are used throughout the process to control the air pressure and velocity and ensure correct fluidization and trouble-free product conveyance. Semi-dense Phase - As an intermediary step between dense and dilute phases, the semi-dense phase conveys materials using a medium velocity. The aim of a semi-dense approach is to achieve a balance between rolling and airborne material. While a system might be run in a semi-dense state to control the rate that materials are delivered into other processes, this method should not be looked on merely as a compromise between higher and lower-powered systems. For certain materials, semi-dense conveying is often more suitable than the either alternative, regardless of delivery rate considerations, which can be adjusted using other parameters and devices.